A Bit Better. Every Day.
Business organisations deal with multiple challenges every single day. And one such challenge lies around processes. And these processes are applied / to be found in every single sphere of life when it comes to the workspace. Many a time, business organisations do not change these processes – if it isn’t broken then why fix it! But this kind of static mindset comes in the way of business growth. And this is where the concept of continuous improvement comes in.
What is continuous improvement?
The term says it all! Businesses like Texmo Industries adopt continuous improvement process:
-
When we want to make incremental improvements,
-
over a period of time so that
-
customers, employees, suppliers etc. in our eco-system reap several benefits.
Continuous improvement is, therefore, all the activities done to make processes, products, and people better in terms of efficiency, and productivity. It can be applied to almost all aspects of the organisation. There are multiple ways in which continuous improvement can be implemented too: Kaizen, PDCA, PDSA and so on. PDCA is plan, do, check, act / adjust. PDSA is plan, do, study, act.
There are quite a few similar approaches to becoming better: benchmarking, lean manufacturing, perpetual beta and so on. The focus here is improvement, which can be achieved consistently, and continuously. As A.P.J.Abdul Kalam said, “Excellence is a continuous process and not an accident.”
One of the stalwarts associated with continuous improvement was Edwards Deming. An American business theorist, Deming is known as the father of the quality movement and is known best for his work in sampling techniques, PDSA, Total quality management, and ‘The Deming System of Profound Knowledge’.
Benefits of Continuous Improvement
integrating flexibility, and continuity in the way our company works has given us many advantages. Continuous improvement (CI) is a holistic process that helps in many ways.
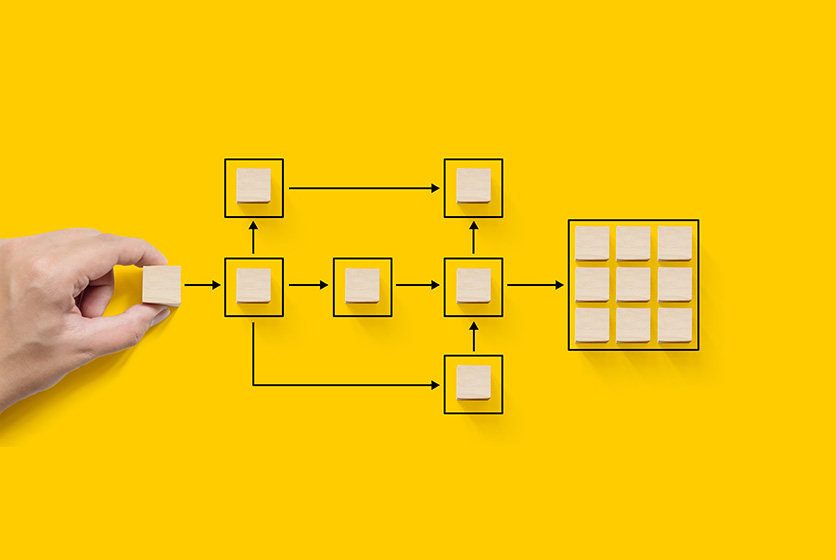
Systematic and streamlined processes: – when processes become streamlined and smooth, then the work output becomes better. High quality becomes repeatable, efficiency is woven into work, and problems are solved more effectively.
All-round improvements: – tools, work environment, methods of working, inter-personal relationships, and every other aspect of the company improves with CI. One of the reasons for this holistic improvement is that CI hinges on feedback. When everybody is inside the feedback loop, course corrections take place quickly.
Cost reductions: – CI helps optimise use of resources and brings down costs because it eliminates wastage. And this has a cascading effect – reduced wastes help optimise costs too and gives Taro Pumps the competitive edge when it comes to delivering value for money.
Culture of innovation: – when the entire team is looking at making incremental changes and small improvements, it all adds up to making things better. This helps an organisation stay ahead of the competition and harness the power of innovation to do better.
And finally, continuous improvement helps an organisation stay agile, resilient, and adaptable. All of them are critical features of any business that wants to stay the course when it comes to keeping their commitments to their customers.
#InterestingInfo
-
Continuous Improvement can be implemented either with an ‘incremental’ approach or a ‘breakthrough’ approach.
-
W. Edwards Deming played a role in Japan’s industrial transformation post World War II.